The Growing Adoption Rate of RFID Technology
It’s hard to avoid the increasing chatter around RFID… it seems like every company is implementing or testing the use of RFID for inventory management, asset tracking, or locationing. News events such as Wal-Mart’s vendor RFID initiative have served to push the adoption rate. As seen in the chart below, expected global compound annual growth for RFID is 11.1% running through 2032!
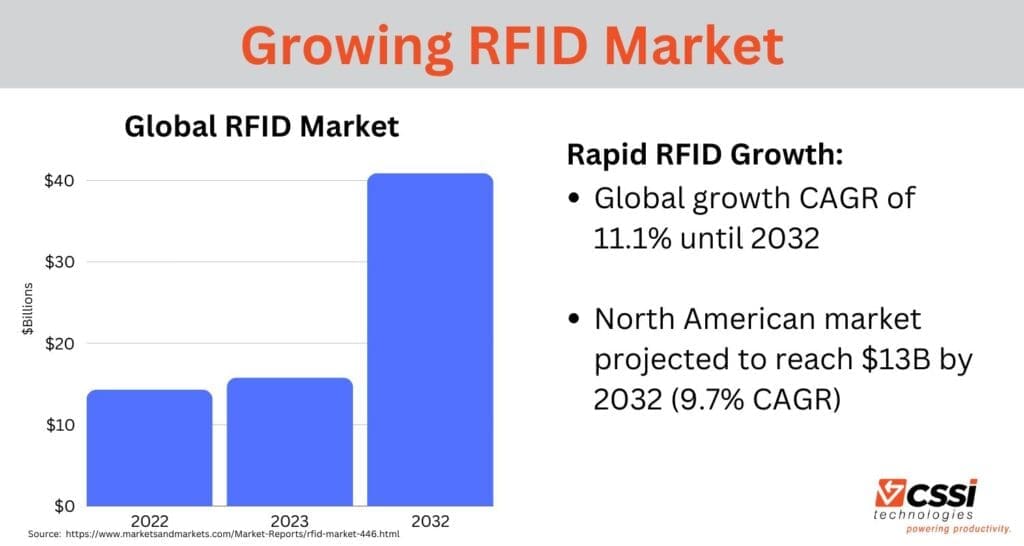
All of this growth is for good reason — RFID technology is exceptionally impactful when applied to the right type of workflow, and when properly implemented. Also, RFID hardware has been improving, and tag costs have been falling.
5 Things that RFID is NOT
While there is a lot of industry excitement around the growing number of applications and use cases for RFID, there are also many misunderstandings and misconceptions (as with any new technology). Let’s address some of those:
1. RFID is Not a Magic Wand

RFID is unlikely to immediately solve all of your inventory management and control issues, certainly not without a lot of work and investment. For example, it seems common for newcomers to envision a system where they can ‘press a button’ and immediately get current inventory counts for an entire facility. For many reasons, several of which are further addressed below, there are likely technical and environmental challenges which will prevent RFID from instantly solving all of your problems.

2. RFID Does Not Solve Problems Caused by Lack of Process or Control
RFID at the core is a means of data capture. This can be extremely valuable for tracking or counting items. However, if your business lacks processes and control, RFID’s impact will be limited. For example, you might install RFID portals in certain doors of your facility, but if users don’t adhere to only transporting items through those ‘choke points’, the system will not be able to capture data. Many RFID projects need to start at a white board to map out the process, and require post-deployment enforcement of processes so as not to undermine the project.
3. RFID is Not Foolproof

What is your acceptable read success rate? It’s important to understand that the successful tag read rate is unlikely to be 100% for a number of reasons (items oriented in the wrong way relative to the reader, or occasional defective tags). Just to be clear, barcode scans will also have a <100% success rate, as missed scans, damaged barcodes, and erroneous scans do happen. A well-run pilot project (see item 4 below) and well thought-out project goals should be able to design around this, but ensuring that the success rate is maximized, and that it meets business needs is important. Pre-deployment testing should enable you to set a reliable expectation for post-deployment read-rate performance.

4. RFID is Not Instantly Deployable
For many applications, RFID can not be deployed without planning, testing, and piloting. By comparison, barcode scanning is faster to deploy because there are fewer potential challenges to successful data capture. RFID requires an investment of time to plan the project and test and fine-tune the system, which involves multiple components which must work in sync: tags, antennas, RFID readers, software, and integrations with your back-end systems.
5. RFID is Not Cost-Effective for Every Application

Sometimes RFID is not the optimal technology to solve your business problem. Whether due to the cost of tags or the amount of equipment which would have to be installed, RFID may be too expensive to create ROI. In some cases, the items to be tracked or the environment are inherently unsuitable for RFID, and result in read success rates which are too low. See: 10 great RFID applications.

Why you need a knowledgeable RFID Solution Partner
With all of the foregoing negatives on the table, it’s important to reinforce that… when RFID is the right fit, it can be massively impactful for your business. That’s why you benefit from working with an experienced solutions partner who can help you to define your business problem, match you with the optimal technology solution, and work with you to test and pilot prior to making larger investments.
Contact CSSI for RFID Help
CSSI Technologies is an experienced data capture, mobile computing, and RFID expert. Our team is available to discuss your workflows and needs, and help you to create successful deployments. To speak with one of our consultants about your potential RFID project, please contact CSSI.