Warehouse Management Systems Improve Operational Efficiency
Warehouse management software (WMS) is a critical tool for companies which maintain inventory and conduct receiving and shipping processes. In a competitive business world, a well-implemented WMS solution enables your warehouse operation to keep up with rapidly changing supply chain needs, improve customer satisfaction, and ensure accuracy. There are many key WMS features, but which are most critical to support your warehouse operations and operational efficiency?
Here are 5 top benefits of warehouse management software
Reason 1. Improve inventory accuracy and visibility
The introduction of barcode scanning and real-time computer information provides a massive improvement in a company’s ability to understand its current inventory positions and locations on a sku-by-sku basis – even in a multiple warehouse operation. The WMS system supports inventory tracking — noting each inventory movement, the quantities available, and quantities picked. This is a light-year improvement over paper-based processes. Further, a warehouse management software enables the easy implementation of cycle counts and general inventory counts, which enable the company to make frequent adjustments and meet inventory level targets. In our fast-moving business environment, this enables the company to rapidly respond when reorders must be placed, or avoid orders when counts are too high.
Reason 2. Save warehouse workers time
A good WMS saves time and supports warehouse efficiency. By enabling the use of mobile computers, the WMS saves the worker time walking back and forth to PCs and accelerates order fulfillment. By putting information in the worker’s hand, it saves time looking for the next action, playing hide-and-seek with inventory, and aimless walking. The right WMS puts the next steps and the necessary info right in the user’s hand, making his or her life easier. More work gets done with fewer delays and frustration.
Reason 3. Reduce inventory tracking and picking errors
A flexible WMS enables the use of barcode scanners for automated data capture. This eliminates handwriting errors which frequently occur in paper-based inventory management processes. The worker can scan to confirm that the correct item is being picked, or that the putaway location is correct. The warehouse management system provides error messages alerting the worker to picking or putaway errors, saving the company from expensive shipping errors and the resulting customer frustration.

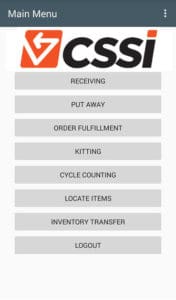
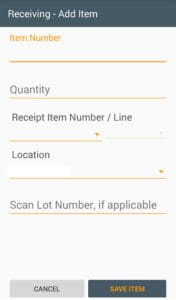
Reason 4. Reduce warehouse employee training time
It’s hard to find workers, and increasingly, the turnover of warehouse workers is more frequent than businesses would like. With that in mind, it’s important to be able to minimize the amount of time required for the warehouse manager to bring a new worker up to productive speed. Warehouse management systems help by providing clear processes and leading the worker through necessary steps. When screen interfaces are easy to understand and ‘next steps’ are clear, it becomes much easier for a new employee to successfully step into a role.
Reason 5. Standardized warehouse processes
WMS software commits your process to a set of code-based rules. It’s easy to overlook, but this requires you to have a well-defined warehouse process in the first place! In implementing a WMS, you will be forced to decide exactly how you want to handle specific jobs. And once implemented, the WMS effectively ensures compliance by your staff by requiring that they adhere to established rules. If a step is required by the WMS, it can no longer simply be overlooked as might happen in a paper-based system.
Bonus Reason: Be Ready For Warehouse Robotics
If our top 5 reasons to use a WMS aren’t enough, here’s a bonus: Warehouse automation is trending, as companies seek ways to improve operational efficiency. Warehouse robotics is an obvious way to improve productivity… but typically, warehouse automation systems and autonomous mobile robots rely on the WMS. Thus, implementing a warehouse management solution now prepares you for future automation innovation.
CSSI Offers a WMS for Dynamics GP
Did you know that CSSI offers warehouse management software developed for companies running the ERP system Microsoft Dynamics GP? WMS by CSSI offers all critical warehouse management features, with the added benefit of customization to meet your company’s unique needs. The WMS platform is highly scalable, and suitable for companies with just a few users all the way up to hundreds of users. Contact CSSI to learn more.