Project in Brief
CSSI created a custom software solution which enabled Universal Stainless to replace a slow and error-prone paper-based QC (quality control) process with a faster, more accurate, and more insightful digital process. This paper-free solution was integrated with barcoding of QC lab samples, and rugged mobile computers.
About Universal Stainless
Universal Stainless is a publicly held manufacturer of semi-finished and finished specialty steel products, and operates with a commitment to provide the best quality, delivery, and service possible. The company operates multiple production facilities in Pennsylvania, Ohio, and New York and serves end markets such as aerospace, power generation, oil & gas, and heavy equipment.
The Status Quo Lab Workflow Process
In Universal Stainless’ status quo manufacturing process, samples called “Slugs” were cut from production materials and sent to the QC laboratory for quality system testing, where they were marked with an ID and went through a receiving process. The samples went through several stations, including one where slugs would be cut into smaller samples called, “Bags.” Once created, a Bag would carry with it the Slug ID and a Bag ID, and would follow a route determined by a planning system that was internally developed by the business. At each station, Bags were tested, and results recorded on paper. The QC team then collected test result papers and manually filed them for the order.
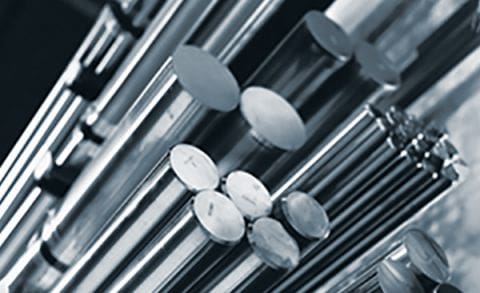
Challenges with the Status Quo Quality Process
There were several problems with the status quo process:
- The QC team was unable to immediately locate items, Slugs and Bags at any point in the process throughout the laboratory. This slowed work down and affected lab efficiency.
- It was difficult to track issues and accuracy as items moved through QA lab, thus limiting accountability.
- There was no data validation. Also, hand-written data led to human error and legibility issues – adversely impacting data integrity.
- There was a lack of reporting capability and visibility of results. Also, loss of paper meant the loss of critical data.
Proposed CSSI Lab Tracking Solution
The CSSI team conducted on on-site multi-day evaluation of Universal Stainless’ status quo lab workflow process, meeting with a varied group of stakeholders to asses the current situation and project goals. CSSI then drafted a detailed proposal for a new sample management process empowered with software and integrated computer hardware. In the new quality management system:
- Bags would be barcoded with Slug ID and Bag ID numbers
- Paper would be eliminated, and data would be collected via handheld mobile computers running a custom browser-based application.
- CSSI proposed Zebra’s MC3300 , a durable and powerful handheld computer with excellent barcode scanning capability and ergonomic interface.
- At each station, data would be collected, and the barcodes would be scanned to ensure a link between the sample and the data.
- The QC lab tracking application would integrate with the planning system via SQL Server database.
Following the customer’s sign-off, CSSI proceeded to create this solution over the course of several weeks in 2018.
Highlights of the CSSI QC Lab Tracking Application
The new quality control laboratory process went live in 2018, with excellent impact for Universal Stainless:
- The new software has amplified accuracy and accountability at each station.
- There is now flexibility in data entry throughout the QA lab, which means each station can accurately enter appropriate data without application modifications.
- The new process enhances the team’s ability to identify and more quickly resolve issues.
- Employee efficiency is improved.
- The software creates automated alerts for the user, which were non-existent in the prior, paper-based process.
- The software includes data validation to ensure good data is captured.
- Factors causing operation delays are now traceable, improving lab efficiency.
- There is now the ability to print barcodes.
- The digitization of quality control data now enables reporting and analytics.


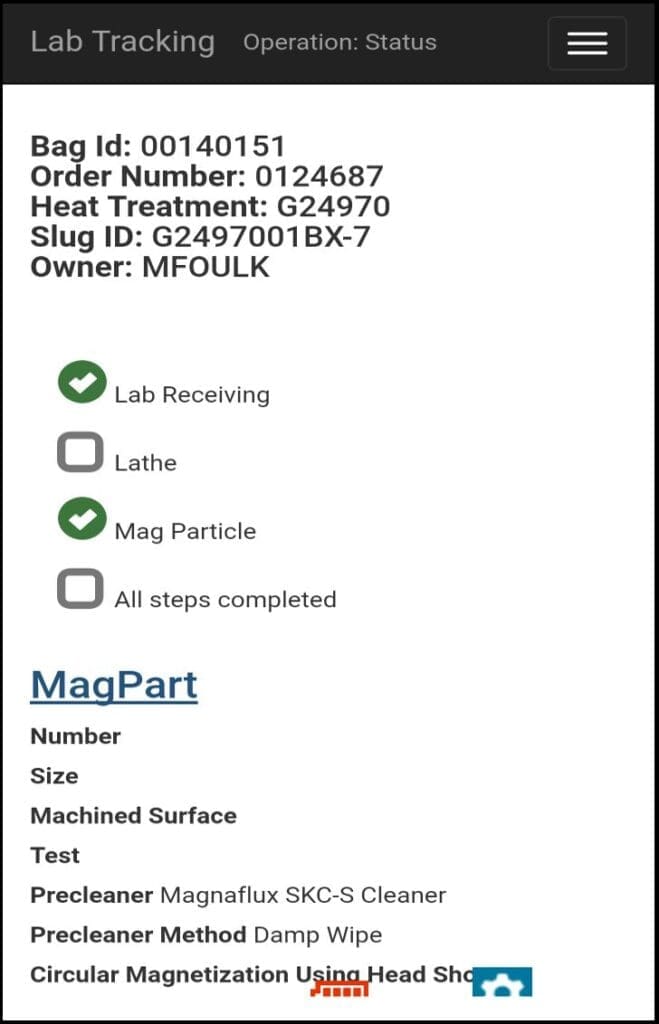
To learn about how CSSI can help you with a custom programming project, please complete the form at right.